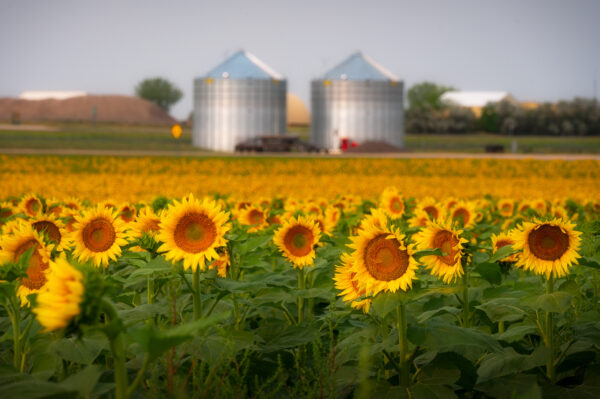
Challenges of a Tribal City: Eagle Butte, SD
State recognized municipalities located within Tribal boundaries can sometimes have unique challenges not seen in a typical small town. The incorporated city of Eagle Butte, South Dakota (population 1,258, of which 88% are American Indian) is the home of the Cheyenne River Sioux Tribe (CRST) Tribal headquarters and lies inside the boundaries of this Tribal nation. The CRST reservation was created in 1889 by the breakup of the Great Sioux Reservation with four of the seven Lakota bands. The reservation is located in north central South Dakota and covers almost all of Dewey and Ziebach Counties. The total land area is 4,266,987 square miles, making it the fourth largest Tribal-owned land area in the United States.
Before the CRST created their own utility, any Tribal-paid improvements made to utilities inside city limits were transferred to the city to maintain. Around 2014, the CRST created the Mni Wašté Water Company and started handling their own wastewater operations and maintenance for the Reservation. As a result, the question of ownership came into play for prior improvements and maintenance to the aging system and who was responsible for future repairs and replacements. With those unanswered questions, there was potential for conflict. For example, at one point in time, one entity hired a contractor to inspect the sewer lines with a camera, resulting in the other entity issuing a cease-and-desist order through their legal counsel. Although the video confirmed that the gravity sewer infrastructure needed repairs and replacements, which was already obvious due to the known collapsed non-working sewer lines, the situation has become contentious because there are two utilities vying for the utility revenue.
The Cheyenne River Sioux Tribe Long Term Group (CRSTLTG) contacted Midwest Assistance Program (MAP) to request their assistance in getting their Tribe and Eagle Butte back on track to make necessary improvements to their infrastructure. Initially, MAP identified possible funding to fix these issues: the State Revolving Loan Fund (SRF), the United States Department of Agriculture Rural Development (USDA-RD), and/or the Indian Health Services (IHS). However, until ownership could be determined, it was impossible to know which entity applies for and manages the funds, since only one utility can apply for and receive funds with the approval of the other entity.
The first thing MAP did was identify all the players and convened a meeting that included representatives from the city of Eagle Butte, CRST, CRSTLTG, USDA-RD, IHS, the Planning District, and the city’s engineering firm. SRF representatives had removed themselves from the discussion, recognizing that Eagle Butte could obtain more grant funds through USDA-RD, considering their Tribal status and that their median household income (MHI) was below 60% of the state’s average. Dialogue could now resume between all the parties to ensure the repairs were made to the systems.
MAP then started helping the city with the USDA-RD application, while simultaneously providing on-site training to the new finance officer. MAP drafted a letter of support from the city to the CRST, asking for their support for the improvements. If support was granted, the city would receive an additional 10% in USDA-RD grant funding, but the CRST has yet to sign the letter.
Despite these setbacks, these entities are all in dialogue to uncover solutions for their utility issues, with MAP’s assistance. As a result, the engineering firm initiated planning and worked on gathering cost estimates, while USDA-RD reopened the old applications. The CRSTLTG is grateful for MAP’s assistance and remains positive that the two entities can work out their differences for the good of their community.
“Your commitment has had a profound impact on our community, and we deeply appreciate the care and attention you’ve shown throughout this process. Your efforts have not only addressed our immediate needs but have also laid the foundation for a stronger, more resilient future for our community.” – Art Rave, Cheyenne River Sioux Tribe Long Term Group
MAP will continue to provide assistance for a long-term solution for the residents of Eagle Butte and the Cheyenne River Sioux Tribe.
This article was funded under RCAP’s EPA Treatment Works 3 – Tribal 23 – 26 grant.
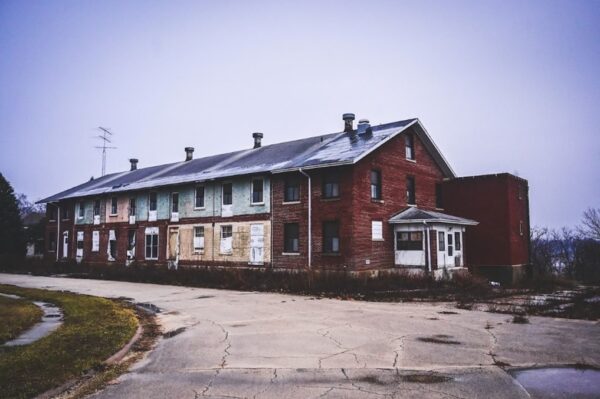
Savannah Army Depot: A new RCAP Challenge
At the end of 2023, the Great Lakes Community Action Partnership (GLCAP) received a referral to start work with the Savannah Army Depot that had been significantly reduced in size. The site was located just outside Savannah, Illinois, on the eastern bank of the Mississippi River in Jo Davies and Carroll County. At one time, the Army Depot was over 13,000 acres and was used for artillery weapons and ammunition testing before its decommissioning by the United States Army in 2000. Currently, there are 30 water and wastewater connections at the Army Depot.
GLCAP Operator Anthony Brown was able to connect with Army Depot personnel to schedule a site visit. Brown began the visit by collecting technical, managerial and financial information from the Depot’s wastewater operator in order to complete an assessment of the facility. During this visit, Brown also shared a flash drive with wastewater resources, which were provided by the RCAP national office through an EPA grant.
Later in the year, Brown returned to the Army Depot to complete a condition assessment of the wastewater system. He walked through the system with the operator and began identifying major issues that needed to be addressed. Through the assessment, it was determined that two major challenges were the presence of I & I (inflow & infiltration) in the system and a loss of sanitary water to the underground environment. He was able to investigate these issues and begin to build a work plan on remediation.
Brown also determined that the wastewater collection system needed to be cleaned and televised and recommended inserting CIP (cast in place) lining as a more cost-effective way to address defects in the system. He is now working with the Army Depot to develop cost identify potential contractors to complete the project. Moving forward, Brown is also assisting the Depot with identifying funding options for these proposed improvements to the wastewater treatment plant.
The Savannah Army Depot project is unique. As a decommissioned site, it presents several challenges, including working with Army Corps of Engineers requirements as well as the shift in population. GLCAP is going to continue to assist the Army Depot and offer any assistance they may need.
This article was funded under RCAP’s EPA Treatment Works 1 Grant.
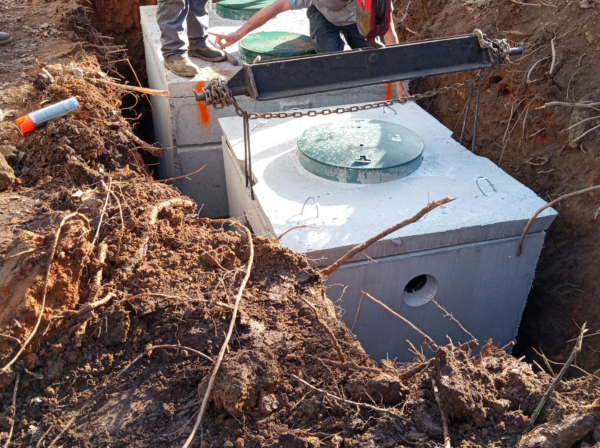
Communities Unlimited Assists with Failing Septic System
A failing septic system can cause numerous issues for a homeowner. It can affect household well water quality and decrease the property’s value. Repairing or replacing a septic system can be costly or require more land than is available. Plus, if the failure results in raw sewage leaving the property or impacting other property, a complaint can be filed with the local health department or state primacy agency. The agency investigating the complaint can then issue enforcement actions under the Clean Water Act and county or state health codes, including declaring the home unfit for habitation, levying fines, or other legal action– leaving the homeowner wondering where to turn for help.
In early January 2024, the Environmental Services Team at Communities Unlimited (CU) was contacted by the Oklahoma Department of Environmental Quality (ODEQ) regarding enforcement action against a homeowner due to a failing septic system. The home’s wastewater was being piped to a hand-dug cesspool at the lower end of his property, and sewage had spilled over onto a neighboring property.
First, a CU Technical Assistance Provider (TAP) gathered resources to share with the homeowner. They connected the homeowner with the US Department of Agriculture’s “504” Housing Program, which could cover the cost of home safety and sanitation repairs, in case the owner met the income guidelines. Although the homeowner did not qualify for the “504”, the CU TAP next provided the homeowner with information about the CU Decentralized Water System loan product, including estimating a monthly payment amount. The CU Lending Team then guided the owner through the process of applying for a loan. In March, the homeowner was awarded a loan of $7,900 to install an aerobic septic system. The system was installed in early April 2024, remedying the ODEQ enforcement action.
Although two other dwellings tied to the cesspool did not meet the eligibility requirements for the CU loan, CU provided information on other resources that might be available to these homeowners.
Finally, the CU TAP facilitated conversations with the ODEQ staff to ensure the court actions initiated against the homeowner would be suspended once the system was scheduled to be installed. The CU TAP also prepared training materials for the homeowner, including a diagram of an aerobic system, how it works, and best practices for operation and maintenance. In addition to sharing information on the Decentralized Water System loan assistance to ODEQ, CU staff provided two training sessions this past year in Oklahoma, focused on decentralized wastewater systems for ODEQ staff and the general public.
Through the work with this homeowner, CU has established a relationship with the staff of ODEQ and is seen as a resource for others in the state with failing septic systems. “Working with Communities Unlimited was a great experience that provided a solution to a longstanding issue DEQ, and the property owner had been dealing with,” said Ryan McIntosh, Environmental Programs Manager – Central Region for ODEQ. “It aided in assisting the individual with access to a septic system that eliminated the discharge of sewage into the environment. Communities Unlimited was the catalyst toward compliance that helped both parties achieve the desired outcomes. Their timely responses and willingness to help was a testament to their core values of truly wanting to improve the lives of people within the communities that they serve.”
The ODEQ provides information on the CU Decentralized Water System Loan to homeowners needing assistance, in the hopes that their failing septic system issues can be resolved quickly to protect the environment. When homeowners in Oklahoma experience septic system issues, they can look to Communities Unlimited for assistance.
This article was funded under RCAP’s EPA Treatment Works 4 – Compliance 23 – 26 grant.
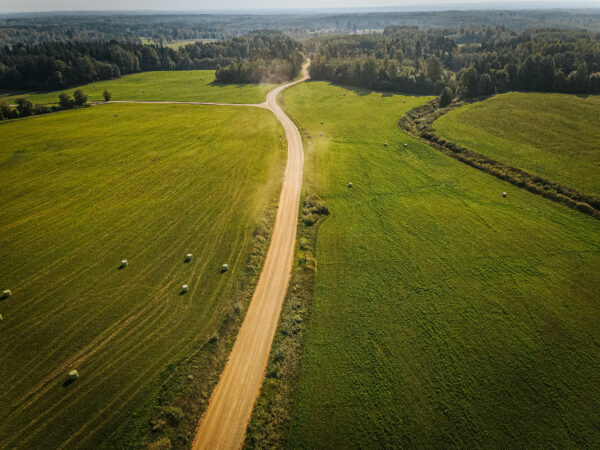
When the Going Gets Rural: Five Challenges TAPs Can’t Escape
Across rural America and U.S. held territories, Rural Community Assistance Partnership (RCAP) Technical Assistance Providers (TAPs) help rural communities navigate complex bureaucracies, secure project funding, and implement infrastructure projects vital to regional economies. However, TAPs face unique challenges that make their jobs incredibly difficult. Despite these challenges, dedicated rural development specialists understand their critical role as a lifeline connecting communities with the resources they need.
From the banks of the Colorado River to the archipelagos of Micronesia, Rural Community Assistance Corporation (RCAC)– the Western RCAP – serves a remarkably diverse region. Regardless of the specific culture or geography, the communities RCAC assists often confront the same basic challenges. Here are five of the most typical challenges TAPs encounter.
1. Tech Time Warp
Due to spotty internet in rural communities, TAPs find themselves dusting off fax machines, googling a tutorial on how to use one, or becoming an in-person courier, hand-delivering documents so the utilities you assist don’t miss critical application deadlines. Advocating for better connectivity is a long-term battle being fought on various levels, but in the meantime, TAPs should be prepared to deal with the same technological frustrations rural water operators face.
2. Capacity
Finding qualified engineers, contractors and other professionals to work in remote rural areas is its own challenge. Communities regularly face overpriced, substandard services and long delays when searching for reliable vendors. TAPs can often expect to spend significant time helping communities navigate the procurement process, vetting bidders, and ensuring that projects are technically sound. TAPs may also find themselves mediating disputes, acting as a watchdog to protect community interests, and providing impromptu project management seminars. Additionally, TAPs may arrive on-site expecting a formal office but instead find yourself working with a few volunteers, juggling their board duties with full-time jobs or businesses or busy lives of their own, including other community leadership roles. In the most basic level, these communities lack capacity for managing major infrastructure projects. Your ability to adapt is crucial.
3. Jumping Through Hoops While Drowning in Acronyms (JTHWDA)
Navigating the labyrinth of federal, state, and local regulations is a formidable task, even for seasoned TAPs. In chronically under-resourced rural areas, the process becomes even more daunting. The alphabet soup of acronyms – RUS, SDWA, CWSRF, TTHM, VOCs and countless others– becomes a second language that takes significant time and effort to master. Understanding the nuances of agency procedures, interpreting timelines and adapting to an ever-evolving regulatory landscape requires specialized expertise and relentless dedication.
Technological constraints can add another layer of complexity; online portals designed to aid the application process often require extensive navigation and troubleshooting due to their design, shifting requirements and occasional technical glitches. The TAP’s ability to navigate these challenges is a vital skill and critical for assisting rural communities to secure the support they need.
4. Perseverance Is Your Friend
Rural communities facing wastewater system failure have no time to spare; when things are not maintained, systems are exposed to potential regulatory fines and public health risks, resulting in cascading economic consequences that can destabilize entire local economies. Securing funding, getting regulatory approvals, and finishing construction projects can take an agonizingly long time. The ability to manage expectations, advocate tirelessly for action, and celebrate even incremental progress is essential for project success and community morale – not to mention your sense of purpose and mental health. Remember: the road to success isn’t always straightforward, and the biggest wins can come from overcoming unexpected setbacks in a slow and steady manner.
5. Empty Pockets, Full Potential
Rural communities bear the brunt of historical neglect, underinvestment, and other structural barriers that continuously limit access to capital and professional expertise. These factors make it tough to keep basic services running and aggravate rural communities’ inherent disadvantages in a playing field heavily skewed in favor of more urbanized, affluent regions.
To effectively tackle these problems, it’s important to understand the historical contexts and inequities that continue to shape rural communities – and their proven track record of finding creative solutions with limited means. This is crucial for crafting strategies that mitigate immediate challenges and pave the way for sustainable development over the long haul.
Rural communities embody a spirit of resourcefulness and determination that can spark remarkable growth when given the right opportunities. By partnering with organizations like RCAP, these communities leverage their strengths, develop strategies for positive change, and energetically build a future where they flourish on their own terms.
This article is funded under RCAP’s EPA NPA 2 2022 – 2024 grant.
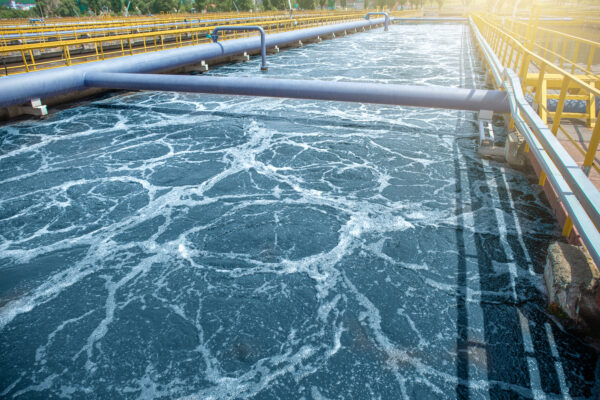
A Primer on Wastewater Utility Rate Review and Increases
Sewer customers may be familiar with the notices, “Due to rising costs, the monthly price of your service is set to increase during your next billing cycle.” So why do so many wastewater utilities struggle to raise rates? Unlike your favorite subscription service, wastewater utility customers do not have the choice of pausing or canceling their membership in response to a price increase and deciding to take their business elsewhere.
Wastewater utilities have a responsibility to safely and reliably treat the wastewater that flows through the plant as well as a responsibility to customers to ensure that the use of funds is lawful and efficient. Proper fiscal management means that revenues not only meet day-to-day expenses but also prepare the system for potential emergencies and future capital projects.
According to the U.S. Department of Labor Bureau of Labor Statistics Consum the cumulative rates of inflation over the last two, five, and ten years are 6.0%, 21.4%, and 31.1% respectively. We should also expect that the costs associated with the safe and reliable treatment of wastewater have also risen during that time. Infrastructure projects constructed in the U.S. during the 1980s are reaching the end of their useful lives and are in need of capital improvements. If typical repair and replacement schedules are not followed, components suffer premature failure, further increasing costs. Wastewater systems can prepare for these capital upgrades with regular contributions to capital reserves, but not all systems have a dedicated reserve fund or, if they do, it may have not have much in it.
A combination of an outdated rate schedule, little to no reserve or emergency funds, and future capital improvement projects places a wastewater system in a financially vulnerable position. Keeping rate evaluations and increases as a regular part of system operation will benefit managers, operators, and customers in the long term. Raising utility rates may not be a popular move and can result in public backlash from customers. However, keeping rates artificially low and postponing rate adjustments is not financially sustainable and will increase future costs, let alone leave the system vulnerable in case there is an emergency. Maintaining clear and consistent communication with sewer customers throughout the rate adjustment process, including opportunities for public input, helps with a smoother transition to potential rate increases.
Whether a rate adjustment is many years overdue or has become part of the regular budget season, the basic steps are the same.
Current rate structure evaluation
First, the system must understand the existing rate structure and evaluate if that should change. Common fee types include a base fee ($/month) and a use fee ($/gallon). These fees can vary for residential and commercial customers. Systems may have other revenue sources such as debt service fees, or funds levied through property taxes. Check your local code for any limitations about the types of rates your system may use.
Financial assessment
A financial assessment is critical to setting appropriate rates. At a minimum, the last three complete years of budget versus actual expenses should be reviewed to understand how money is moving through the system and what are common expenses as part of operations.
Customer assessment
Customer data must also be reviewed for rate adjustments. Critical questions such as, “How many customers are there, and how much are they paying?” should be asked during this review process. If use fees are applied based on meter data, are there use patterns? Are residential and commercial customers billed differently? Create a picture of the types of customers using the system and what kind of bills they are currently paying. Does this reflect the goals of the municipality and the utility?
Future projections
In concert with the financial and customer assessments, utilities should also consider the future use of the system. Are the expenses expected to change significantly due to capital projects? Is the number of customers expected to stay the same or change? Be critical when reviewing population data since customer bases may be in decline, but rates could be calculated on number of potential users instead of actual users. Use local knowledge and data to make projections for cost and use.
Rate options
With an understanding of total revenue under the current rates coupled with projections for total revenue needed, the difference shows how much additional revenue is needed to maintain sustainable operations. The board of the wastewater system must determine how to produce the additional revenue using available rate structures. Increasing base fees provides a more reliable revenue source but may be unfair by charging all customers evenly, whereas increasing use fees gives customers the most control but leaves the system more susceptible to revenue shortfalls if usage decreases. Considering three to five different rate options can help boards and customers evaluate the pros and cons of different strategies for meeting the system’s expenses.
The annual budget process is a natural opportunity for wastewater systems to assess their financial needs and make necessary adjustments. Just as expenses are consistently rising, sources of revenue need to keep up. Regular rate increases can be intimidating to implement but are a foundation of financial sustainability in any wastewater system.
For additional information, check out our rates guide and our eLearning on rate setting.
This article is funded under RCAP’s EPA NPA 2 2022 – 2024 grant.
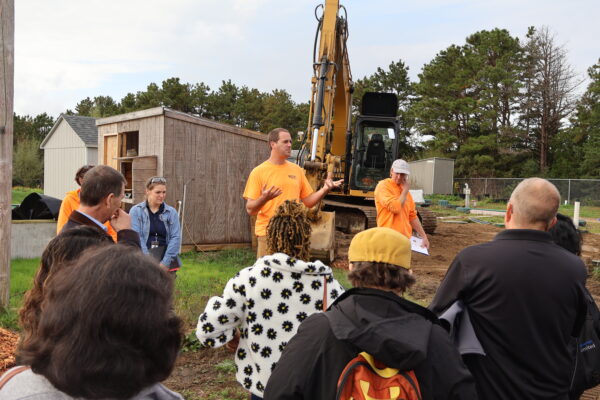
When the Going Gets Rural: Five Challenges Technical Assistance Providers Can’t Escape
Across rural America and U.S.-held territories, RCAP technical assistance providers (TAPs) help rural communities navigate complex bureaucracies, secure funding and implement infrastructure projects vital to regional economies. However, TAPs face unique challenges that make their jobs incredibly difficult, to put it mildly. Despite the headaches, dedicated rural development specialists understand their critical role as a lifeline connecting communities with the resources they need.
From the banks of the Colorado River to the archipelagos of Micronesia, Rural Community Assistance Corporation (RCAC) – the Western RCAP – serves a remarkably diverse region. Regardless of the specific culture or geography, the communities RCAC assists often confront the same basic issues. Get ready, because here are five of the most frustratingly typical challenges TAPs encounter – and why overcoming them requires a whole lot of grit.
1. Tech Time Warp: Back to Y2K!
Do you think the small-town wastewater operator ghosted you? Well, maybe they did – or maybe they’re dealing with spotty bandwidth. You might find yourself dusting off your fax machine – or googling a tutorial on how to use one – or becoming an in-person courier, hand-delivering documents so your partners don’t miss critical application deadlines. Welcome to the analog shuffle! Advocating for better connectivity is a long-term battle being fought on various levels but, in the meantime, prepare to deal with the same technological frustrations rural water operators face.
2. Capacity – Where Did Everybody Go?
Have you ever tried to find a qualified engineer in a town smaller than your high school? You might arrive expecting a formal office but instead find yourself working with a few volunteers juggling their board duties with full-time jobs or businesses and busy lives of their own, including other community leadership roles. Imagine the person who organizes the town festival also taking a crash course in cryptic agency guidelines and cumbersome grant applications. On the most basic level, these communities lack the homegrown capacity for major infrastructure projects.
Finding qualified engineers, contractors and other professionals to work in remote rural areas is its own challenge. Communities regularly face overpriced, substandard services and long delays when searching for reliable vendors. Expect to spend significant time helping communities navigate the procurement process, vetting bidders and ensuring that projects are technically sound. You may also find yourself mediating disputes, acting as a watchdog to protect community interests, and providing impromptu project management seminars. Your ability to adapt is crucial!
3. Jumping Through Hoops While Drowning in Acronyms (JTHWDA)
Navigating the labyrinth of federal, state and local regulations is a formidable task, even for seasoned TA providers. In chronically under-resourced rural areas, the process becomes even more daunting. The alphabet soup of acronyms – RUS, SDWA, CWSRF, TTHM, VOCs and countless others– becomes a second language that takes significant time and effort to master. Understanding the nuances of agency procedures, interpreting timelines and adapting to an ever-evolving regulatory landscape requires specialized expertise and relentless dedication.
Technological constraints can add another layer of complexity; online portals designed to aid the application process often require extensive navigation and troubleshooting due to their design, shifting requirements and occasional technical glitches. The TAP’s ability to navigate these challenges is a vital skill and critical for assisting rural communities to secure the support they need.
4. Time Isn’t Your Friend, Perseverance Is
Rural communities facing wastewater system failure have no time to spare; when things really start to stink, they’re exposed to potential regulatory fines and public health risks, and resulting cascading economic consequences that can destabilize entire local economies. Securing funding, getting regulatory approvals and finishing construction projects can take an agonizingly long time. The ability to manage expectations, advocate tirelessly for action and celebrate even incremental progress is essential for project success and community morale – not to mention your sense of purpose and mental health. Remember: the road to success isn’t always straightforward, and the biggest wins can come from overcoming unexpected setbacks!
5. Empty Pockets, Full Potential
The fundamental challenge lies in a critical resource scarcity – a symptom of deep-rooted structural inequalities that favor metropolitan centers at the expense of rural zones, which is a worldwide phenomenon. Rural communities bear the brunt of historical neglect, underinvestment and other structural barriers that continuously limit access to capital and professional expertise. These factors make it tough to keep basic services running and aggravate rural communities’ inherent disadvantages in a playing field heavily skewed in favor of more urbanized, affluent regions.
Think of it this way: smaller communities often receive fewer resources up front, making it harder to attract businesses, skilled professionals and even essential workers. This creates a negative feedback loop where the lack of resources leads to even fewer resources. Over time, it becomes incredibly challenging for these communities to compete on their own, even when they have amazing ideas or potential.
To effectively tackle these problems, it’s important to understand the historical contexts and inequities that continue to shape rural communities and their proven track record of finding creative solutions with limited means. This is crucial for crafting strategies that mitigate immediate challenges and pave the way for sustainable development over the long haul.
Rural communities embody a spirit of resourcefulness and determination that can spark remarkable growth when given the right opportunities. By partnering with organizations like RCAP, these communities leverage their strengths, develop strategies for positive change and energetically build a future where they flourish on their own terms.
This article was funded under RCAP’s EPA Wastewater 2022 – 2024 grant.
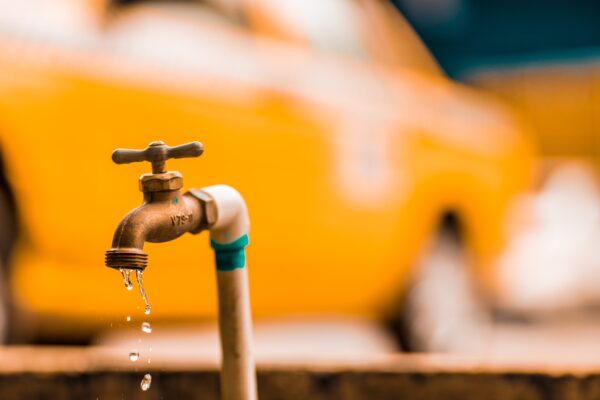
Wastewater Maintenance: Drawdown Pump Test
How do you respond when your car reminds you it is time for a check-up? Or when your calendar sends a reminder that it is time for a doctor’s appointment or teeth cleaning? Nearly everything, from our bodies to our appliances, requires maintenance to survive without breakdown. Preventative care is usually less expensive than costly repairs when breakdowns occur, so performing up-front routine maintenance can save money, time, and energy.
Maintaining your community’s wastewater system will increase its sustainability, further addressing aging infrastructure, limited funding, and increased populations and demands. Failure to upkeep your system will result in system failure and create compliance issues. One of the major issues could be the effluent not meeting permit standards and, most importantly, the community’s wastewater not being treated correctly, thus creating a public health issue.
One solution to protect and maintain your community’s wastewater system involves completing a drawdown pump test at the lift station.
How to perform a Pump Drawdown Test:
1. Determine the pump rate in gallons/minute.
What is the size of the lift station? (diameter in feet or length, width or depth)
To find the pump design size/capacity information, look in the manual or plans of the lift station.
What is the influent rate without the pump running?
You should calculate the influent rate with a stopwatch, rod, or meter tape marked in feet and inches. An electronic water level meter tape is a more expensive but straightforward method of gauging depth changes. You can determine the cubic footage over a set period.
Turn the pump off and use the rod and stopwatch to measure the water rise in a set time. This will establish the cubic feet per minute. Multiply it by 7.48 gal/ft3to compute gallons per minute influent. This is the influent rate without the pump on.
What is the drawdown rate with only one pump running?
Turn the pump on and analyze the drawdown in water over the same set period with the pump running. This is the drawdown rate with the pump in operation. Determine the cubic feet per minute and gallons per minute. Add the influent rate to the calculated drawdown rate to calculate the gallons per minute pump rate.
2. Determine the effectiveness of the pump.
What is the percentage of efficiency?
Convert the design capacity pump rate (rated capacity) to gallons per minute.
Divide the pump rate you calculated by its rated capacity and multiply it by 100. This is the percentage of efficiency.
The following rate calculations are for a circular wet well:
Influent Flow Rate Calculation
Where D is the diameter of the well, and R is how much the water level rises (in feet) in one minute.
Initial Drawdown Rate Calculation
Where D is the diameter of the well, and F is how much the water level falls (in feet) in one minute.
Pumping Rate Correcting for Influent Flow
Pump Rate = Drawdown Rate + Influent Rate
Pump Efficiency Calculation
Performing a drawdown pump test will calculate your pump’s actual pumping flow rate and diagnose possible issues with your pumping system. Additionally, this test will determine if your lift station(s) are functioning efficiently. It is best practice to examine wastewater pumps at least twice yearly to expose operating conditions changes.
Safety Warning:
Disconnect and lock out the power before servicing equipment. Review the manual to be aware of any safety guidelines before starting.
This article was funded under RCAP’s EPA Treatment Works 2022 – 2023 grant.
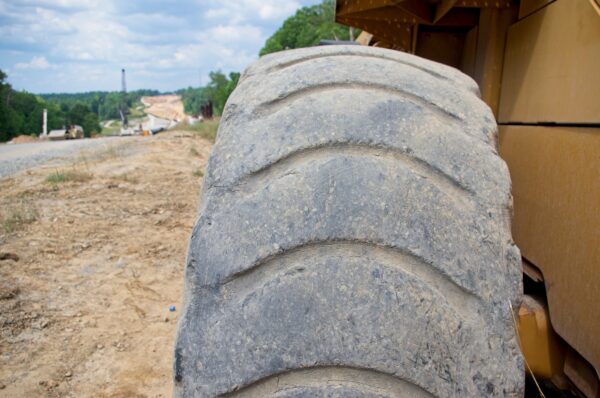
Water and Wastewater Utility Asset Management: Vehicles
There are innumerable articles, webinars, books, training sessions and publications that address asset management for water and wastewater utility systems. Though philosophies and frameworks vary, all of them essentially say, “Know what you have.” When we think about utility assets, we tend to picture structures such as pump houses, treatment plants, tanks, vaults, basins, the underground facilities and piping. These are easy to consider as “assets”. Keeping track of them involves building plans, up-to-date maps, maintenance history, and more. Unfortunately, though managers try to keep detailed records and maintenance plans for facilities, when capturing inventory for rate setting, vehicles used for many aspects of running the utility system often receive less attention.
If the system is large enough, there may be established fleet management personnel, procedures, recording systems, maintenance records, and maintenance schedules. In smaller systems however, where employees wear multiple hats or vehicles are used across a variety of purposes, record keeping and maintenance schedules may be in the hands of individuals that may not prioritize the care of the cars, pick-ups, dump trucks, tankers, vac-trucks, or even backhoes, tractors, mowers (depending on the manner in which such equipment is categorized for each system) with equal consideration of other equipment used in moving and treating water/wastewater. Hearing “I wasn’t the last one to use it” is not uncommon. Sometimes forgotten is the fact that the SUV used to travel to a water training session, or the tractor with a finishing mower to keep the wellhouse lot tidy, are both legitimate uses for utility system purposes. Keeping track of the vehicles can be made easier with the use of fleet maintenance software and programs, and a dedicated person with an aptitude for computers and data entry to maneuver through those systems. Of course, that is if the utility can afford such tools, which are generally quite pricey, and can be cumbersome for some fleets.
An alternative suggestion is to appoint one single person to oversee vehicle records, maintenance schedules, and other paperwork. This employee does not need to be the one performing the actual wrenching, lubing, and repair on the vehicles; the mechanical work can be contracted out. Documentation and recordkeeping can be done through a homemade spreadsheet or database, and a computer folder to hold scanned materials on each vehicle. Of course, some papers, certificates, and documents (titles, bills of sale, registration, insurance, etc.) are required to be kept in hard copy form, so an actual file folder (such as an expanding folder or accordion file keeper) for each vehicle is recommended. Keep the folders in a single location that is known and accessible to more than one employee.
Other items that are beneficial to place in a vehicle’s folder, whether real or electronic, include: receipts for all parts and services, notes on uses and users, comments and complaints from operators, and photographs. Speaking of pictures, be sure to take photos when the vehicle is first acquired, from each side and multiple angles, as this provides a historical record if damage occurs, or other future uses. Finally, provide each vehicle with a distinct identifier, be it a number or alpha-numeric designation. No need to be overly complicated with it. Do not reuse identifiers from previous units that have been removed from the fleet – confusion will ensue, and running out of numbers is generally not an imminent worry. Maintaining the care of these vehicles is a necessary and continuous component of any water and wastewater utility.
This article was funded under RCAP’s Treatment Works 2022 – 2023 grant.
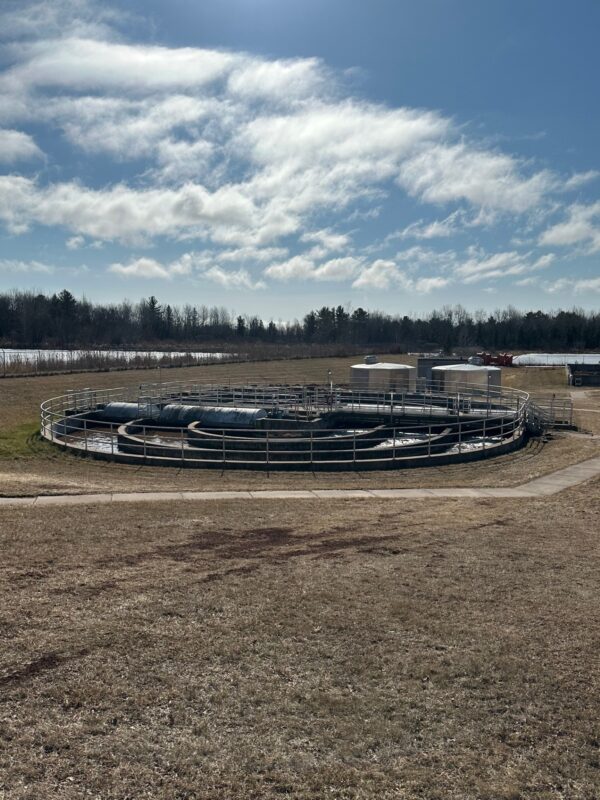
Red Cliff Wastewater Treatment Plant Compliant Treatment Process
Red Cliff Public Works Department, which includes the Red Cliff Band of Lake Superior Ojibwe’s wastewater treatment plant, is located on the southern shores of Lake Superior. The Wastewater Treatment Department is run by the Public Works Administrator, along with two operators. They are also hiring a new Assistant Director.
Aided by the many years of knowledge between the experienced Public Works Administrator and Lead Operator, the utility has been making great strides to get the Wastewater Treatment Department in compliance with US Environmental Protection Agency (EPA) regulations and keep it there.
When the administrator came on board, the first task he undertook was to lead the utility to completion of the EPA’s Administrative Order of Compliance. The administrative order required a set of tasks and responsibilities to be conducted within two years. This was accomplished in nine months.
One of the many positive changes made on the way to compliance was moving the chemical feed of aluminum sulfate to the splitter box prior to effluent entering the clarifiers. By injecting the aluminum at the splitter box, the additive now has enough “contact time” to assist the wastewater with phosphorus and ammonia removal via the process of flocculation. As the particles combine, they become floc and settle out. The better the flocculation, the better the overall effluent, with less phosphorus and ammonia.
Let’s review the wastewater treatment process at Red Cliff:
First, we have our influent, which is pumped to the treatment plant from lift stations and gravity-fed sewer lines throughout the collection system. As the wastewater begins its process, it starts off at pretreatment, where it passes through a bar screen which is used to remove large physical materials and debris.
From the bar screen, the wastewater continues through a fine screen where smaller debris is removed.
From there, the wastewater passes through a grit removal process that helps remove the finer granular matter from the wastewater.
As the wastewater makes its way through the grit removal process, it now enters the oxidation ditch. This is where the raw wastewater is introduced to microorganisms and the microbiology portion of treatment begins. It is the wastewater operator’s job to keep the microorganisms happy and healthy. The dissolved oxygen (DO) must be monitored and set at the correct level to keep the tiny critters alive, but not give them too much DO where they won’t eat any of the biological matter in the wastewater to keep the treatment process going. There is a fine line that needs to take place with the microorganisms as they play a major role within the wastewater treatment process. The biology and microbiology that take place within wastewater treatment is just one of the many processes that most people do not know happens.
From the oxidation ditch, a portion of the mixed liquor is pumped back to the oxidation ditch, also known as Return Activated Sludge or RAS. RAS has a healthy batch of microorganisms which will be used to jump-start the natural microbiologic treatment process.
Now, as wastewater has been introduced to the microbes and natural matter has been removed, aluminum sulfate has been added to aid in phosphorus and ammonia removal and the effluent makes its way to the clarifiers.
As the alum interacts creating floc, this matter will settle to the bottom which creates a clearer effluent.
From the previous treatment process, the final product, known as effluent, is sent through an ultraviolet light bank which neutralizes any pathogenic organisms. This process prevents any remaining pathogens from being able to reproduce if they have made it through the treatment process.
Numerous steps are taken to ensure the effluent is safe and meets all the EPA’s stringent standards before final discharge. Many samples, analytical data, and test results are collected, reviewed, and recorded before the final effluent is discharged. Biosolids created during the treatment process are pumped to the utility’s reed beds, where they are dewatered and stored. The reed beds can dewater natural materials many times the weight and size of the reeds themselves. Through a collection of underdrains, any liquid collected is sent back to the top of the plant to be reintroduced and begin the process all over again.
Through the hard work of the utility’s staff and the partnership with RCAP, the Red Cliff Wastewater Treatment Plant has met and continues to meet the requirements and standards needed to stay in compliance.
This article was funded under the EPA NPA 2 22 – 24 Grant.